Safety First
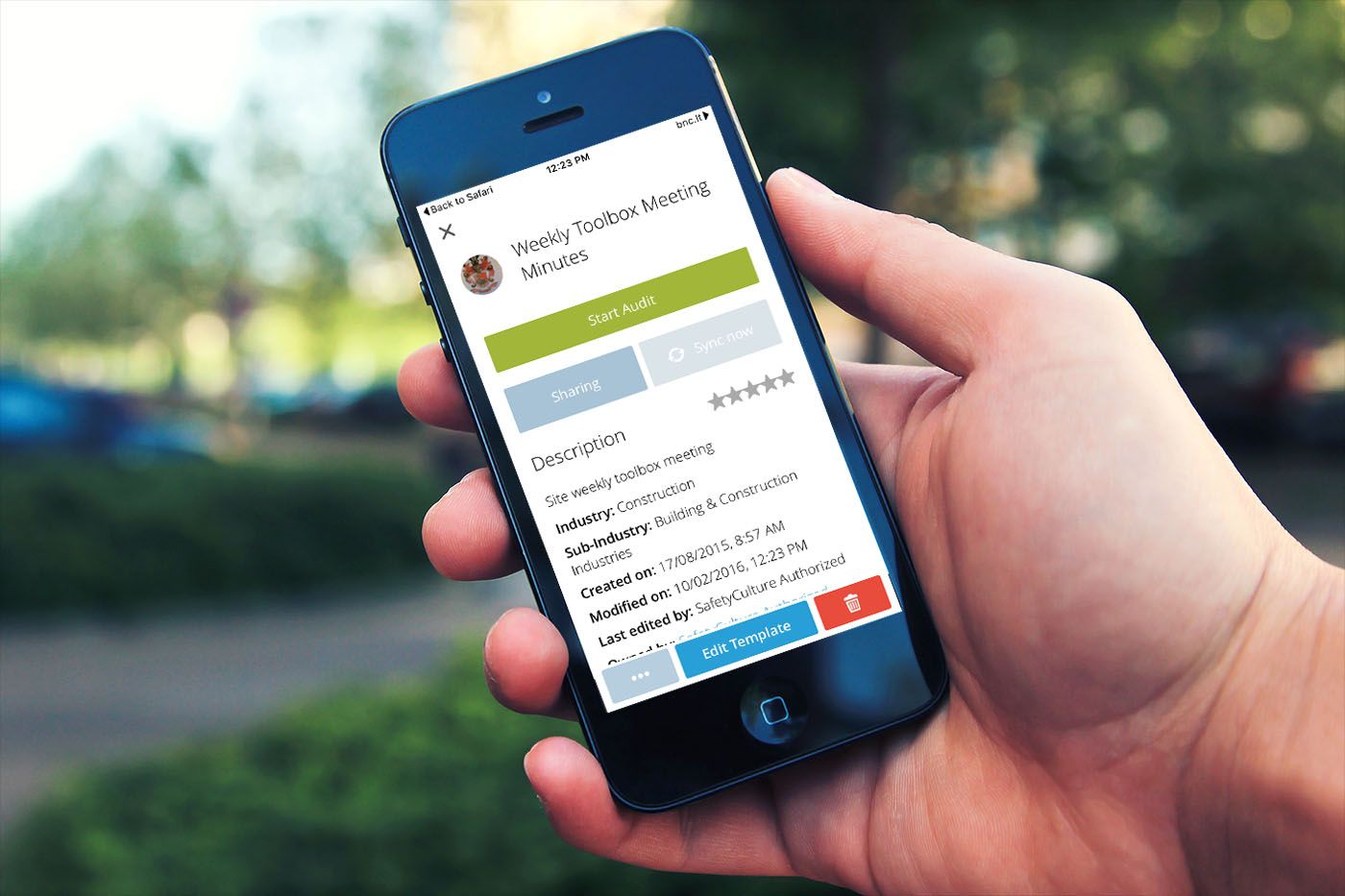
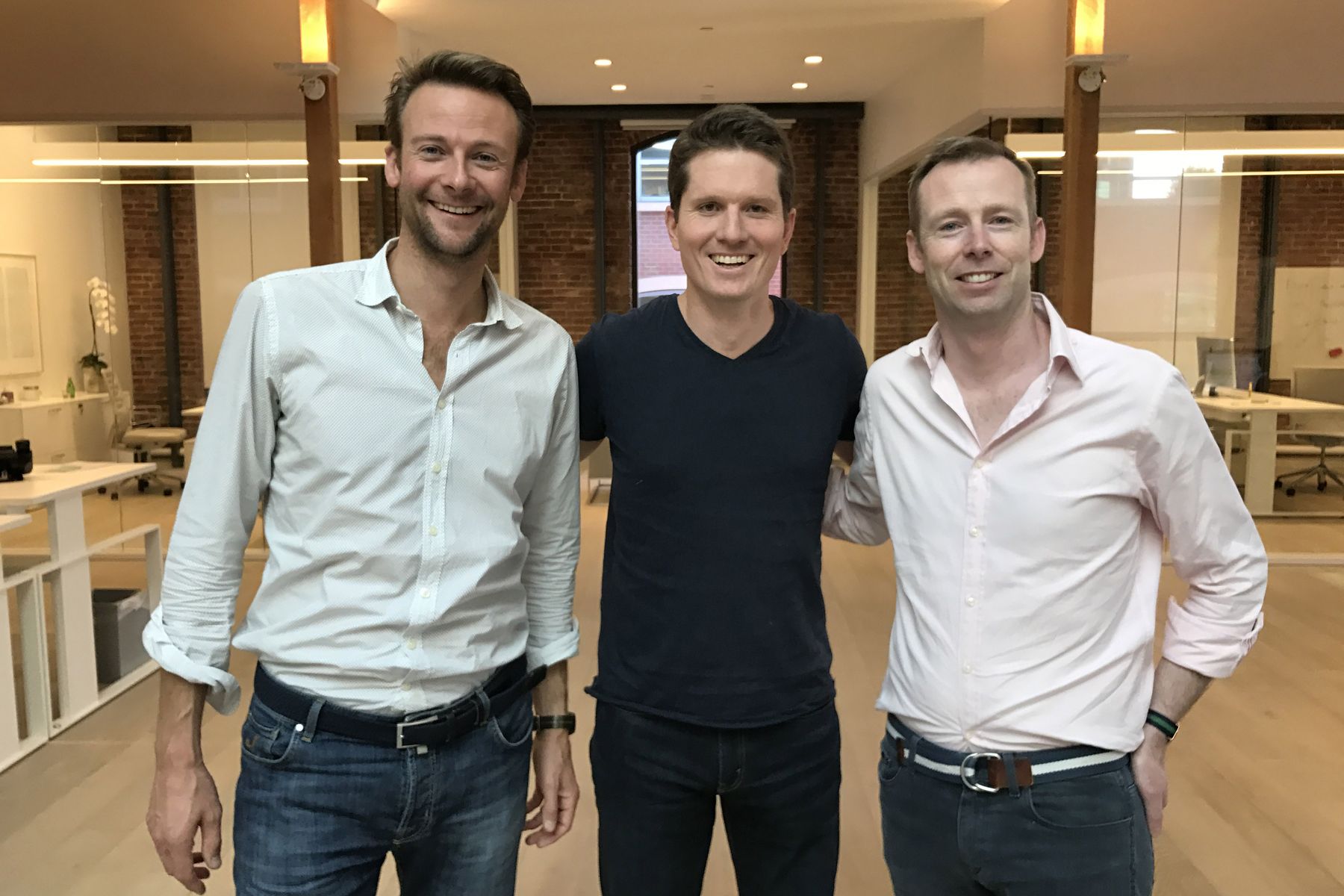
Samsung recently made the unprecedented decision to recall—and ultimately end production of—its Galaxy Note 7 smartphones, which were exploding due to faulty batteries supplied by an affiliate. Ever since the first device explosion, the company has insufficiently tried to fix the problem, and the consequences have been swift: its brand has taken a significant hit, multiple customers are suing the company, and investors have knocked off over $17 billion from the South Korea-based company’s market cap.
The Samsung recall illustrates a growing need for companies to focus on improving internal quality and safety procedures and reinforces the need for testing and inspection. This is true for products like the Galaxy Note 7, but extends to inspecting and auditing everything from the safety of construction workers and food in supermarkets to the maintenance of factory equipment and airplane parts. Nowadays, safety and quality inspection underpins everything we do and all the products and services we use.
The pressure on companies to increase quality assurance and worker safety has led to the creation of a massive industry: the testing, inspection and certification market amounts to a staggering $120-150 billion every year and has grown in a secular way by roughly 10% per year for the last decade – a number that will likely accelerate. In-house specialists currently perform approximately 60-70% of this work while the remainder is outsourced to more than 2,000 service providers who employ 600,000 people. The three largest outsourcing providers — SGS, Bureau Veritas and Intertek — alone generate roughly $14 billion in combined annual revenue and represent a market capitalization of roughly $32 billion, though they are only familiar to industry insiders.
The safety and quality assurance industry will continue to grow and we expect its growth will accelerate as a result of four major trends:
Increasing Product and Supply Chain Complexity Across the Globe
New products become more complex and customized while at the same time supply chains are more global and fragmented than ever before. While this means that manufacturers are more likely to lose control over their products, they still remain responsible for their efficacy, quality and safety. As a result, manufacturers need to continuously improve their testing and inspection capabilities to help them stay compliant with quality, performance and regulatory standards.
Quicker Speed to Market
Shorter product lifecycles and reduced development times require faster and more accurate product development support. Today’s companies, particularly those in highly competitive industries, are under constant pressure to improve and expedite their internal testing and make their inspection processes available on-the-go to enhance the time and resources needed to comply with regulations and standards.
Increasing Number of Regulations
Whether they follow external regulators’ rules or self-impose them, companies must ensure that their products and services consistently meet a broad range of standards. Non-compliance is not an option, as the associated financial, reputational and ethical costs are astronomical and the consequences can be irreversible.
Growing Demand for High Quality and Accountability Expressed in the Public Domain
When deciding on a purchase, today’s consumers are increasingly focused on buying from a manufacturer that not only provides a high-quality product and excellent customer service, but also manages its production and supply chain in a sustainable and safe way. This requires a better understanding of all of the complexities underlying their product and supply chain issues, as well as modern testing and inspection tools.
A Significant Shift is Changing the Industry
Today, companies have less-than-optimal options for reliably and efficiently controlling their equipment, processes and supply chains. Factory employees often use pen and paper to note defective machinery or assess product quality — a hugely inefficient, non-standardized and time-consuming process that gives companies extremely limited visibility into what’s happening and what needs to be fixed. The alternative is to hire external service providers to inspect processes or equipment, but third-party providers are often expensive and require the companies to give up control over the inspection process.
The increasing proliferation of mobile devices has led to the emergence of mobile testing and inspection software vendors that we believe have the potential to revolutionize this hidden and large market and lead to material improvements in safety and quality across industries. Cloud-based mobile audit apps do not only make it easier to capture all required information, they also store the data in one central location and facilitate benchmarking and collaboration between team members. By bringing safety solutions into the hands of workers, mobile apps help to increase employee engagement and to ingrain safety into the workplace culture and the employees’ workflows, which ultimately turns the app into the system of record for many critical processes.
SafetyCulture Emerges as a Leader in the Mobile and Cloud World
Over the past few years, we have actively tried to find a company that understands all of these shifts within the broader safety and inspection industry and can seize this huge market opportunity. Most of the potential investments we evaluated, however, lacked a clear long-term product vision and did not offer a scalable solution that was applicable to different processes, companies or industries.
A year ago, we met Luke Anear who told us the story of SafetyCulture, a safety and quality inspection SaaS company that he founded in Australia back in 2004. We were immediately impressed with his long-term vision for iAuditor, the company’s four-year old safety and inspection app. First and foremost, iAuditor provides an excellent, frictionless user experience for the employee, which is complimented by comprehensive reporting and analytics capabilities. This end-user focus has driven the widespread, bottom-up adoption of the app across blue chip clients like Coca-Cola Amatil, Coles Supermarkets, GE, Accor Hotels, Singapore Airlines and BHP Billiton — just a few of the 6,000 organizations that have used SafetyCulture to help roughly 100,000 users complete more than 30 million safety and quality inspections.
Early on, Luke, like many other Australian SaaS founders, borrowed a page from Atlassian’s book: the iAuditor app was (and remains) available free of charge on the iOS and Android app stores globally, which allowed SafetyCulture to expand to 180 countries within months and use a low touch sales model to upsell premium features. Luke was so successful that when he met Scott Farquhar, Atlassian’s co-founder and co-CEO, a few years ago, Scott immediately bought into SafetyCulture’s vision and business model and decided to invest his personal money and time into the company.
This is why we are proud to partner with Luke and lead a $23 million funding round in SafetyCulture. The financing will help the company execute on their ambitious product roadmap, augment the team, expand SafetyCulture’s commercial footprint globally and harness the big data benchmarking opportunity. Ultimately, the company will be in a unique position to offer advanced risk profiles for commercial liability and workers’ comp insurance based on the unique proprietary datasets about its clients’ quality and safety records. We are excited about helping SafetyCulture achieve its goal of giving every company access to the best mobile safety management system available and we look forward to supporting Luke and his team as they revolutionize this massive and hidden market.
Published — Oct. 18, 2016